Integrating Accounting into Maintenance ERP: The Key to Centralized Efficiency in Aviation
In the dynamic field of aviation, the synchronization of maintenance operations with financial systems is not merely a convenience—it is a strategic imperative. Traditionally, maintenance and financial operations in aviation have been siloed, leading to inefficiencies and a higher likelihood of error. This separation often means duplicated efforts, inconsistencies in data, and delays in financial reporting. However, incorporating accounting directly into a maintenance Enterprise Resource Planning (ERP) system streamlines processes, enhances accuracy, and provides a comprehensive view of organizational health. Here’s how integrating accounting into your maintenance ERP can transform your aviation operations.
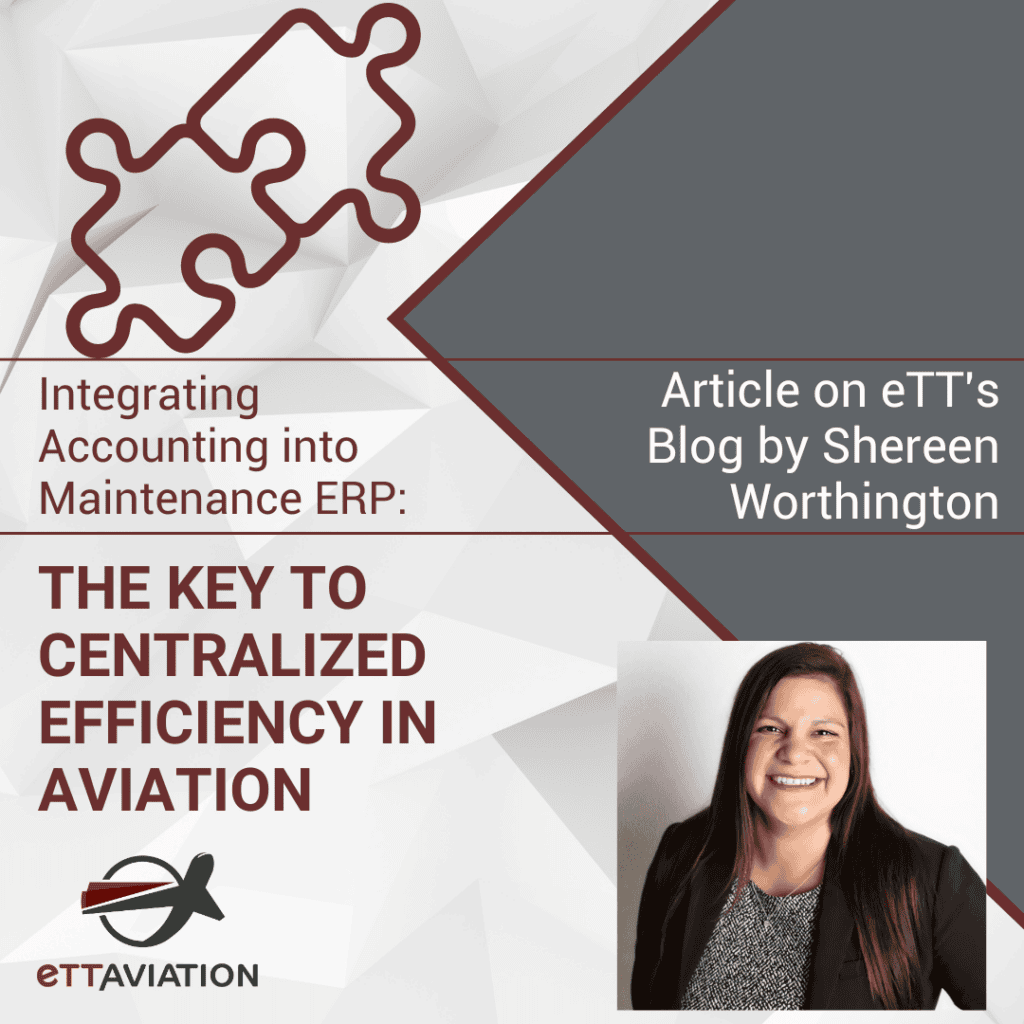
The Holistic Approach to Maintenance and Finance
A maintenance ERP with integrated accounting functions acts as a central nervous system for aviation businesses, connecting different facets of operations—from purchasing and inventory management to accounts payable and receivable, general ledger entries, and budgeting. This integration ensures that all financial aspects of maintenance operations are captured in real-time, providing a seamless flow of information across departments.
- Purchasing and Inventory Management: When maintenance requires specific parts, the purchasing process automatically ties into the financial system, updating expenditure and adjusting inventory levels. This real-time updating prevents discrepancies between physical stock and financial records, ensuring that purchasing budgets are directly aligned with maintenance needs.
- Accounts Payable and Receivable (AP/AR): Integrating AP/AR within the maintenance ERP allows for an immediate reflection of expenses and income. When a maintenance job is completed and invoiced, the system automatically updates the receivables, improving cash flow management. Conversely, when a part is ordered, the payable is immediately logged, ensuring that financial obligations are transparent and managed efficiently.
- General Ledger (GL) Entries: By automating GL entries directly linked to maintenance activities, aviation businesses can ensure financial accuracy and significantly reduce the time spent on month-end closings. This automation helps in maintaining a clean ledger with real-time updates, providing crucial financial insights at any point in time.
- Budgeting: With all financial transactions integrated into the ERP, budgeting becomes more precise and less time-consuming. Managers can see actual spend versus budget in real-time, allowing for more proactive financial management. This visibility helps in making informed decisions about future maintenance activities and financial planning.
Enhanced Compliance and Reporting
Compliance with industry standards and financial regulations is streamlined through an ERP system that combines maintenance and accounting. Financial reports are always backed by up-to-date and accurate data, reducing the risk of compliance issues. Moreover, with robust reporting capabilities, stakeholders can receive tailored reports that provide insights not just into financial health but also into the efficiency of maintenance operations.
Strategic Decision Making
Integrating accounting into maintenance ERP enables strategic decision making. Managers can analyze comprehensive data to understand the financial impact of maintenance activities. This analysis can lead to more strategic planning, such as identifying areas where cost savings can be made without compromising safety or quality.
Conclusion
The integration of accounting into maintenance ERP systems marks a significant advancement in aviation operations management. This unified approach does not merely keep the financial score but actively contributes to more efficient, compliant, and strategic operations. For aviation companies looking to enhance operational efficiency and financial transparency, integrating accounting in their maintenance ERP isn’t just an option—it’s a necessity.
In embracing this integrated approach, aviation companies can ensure that they are not just keeping up with the industry standards but are setting new benchmarks for operational excellence.